Every one of my estimates of when our new house will be completed has been laughably optimistic. At first it was going to be by the end of last summer. Then it was going to be the end of November. And then it was the end of February. Now it’s the end of May. The difference now is that the buyers of our old house have a one-year lease on a house that ends at the end of May. Our neighbor, the real estate broker who handles the rental of that house, told me there would be no problem extending their lease, but I’m treating it as a hard deadline.
The last inspection (way, way back in December) found issues with framing and plumbing testing. The framing repairs have been completed. The well guy and the electrician have temporarily powered the well pump so the plumber can pressure test the supply lines. The plumber came out last week and fixed a couple of leaks. I, however, have not managed to repair leaks in the work I have done.
We have double water filters in our current house for sediment from the well. I assume the new well’s water will also have sediment, so I connected a pair of filters for the new house, one for coarse sediment and one for fine sediment. They are connected with a glued PVC section that is attached to threaded fittings on the filter housings. The first time we pressurized the system, my connections leaked. So I hacksawed them apart and replaced them. This time I used Teflon tape as the plumber and some online resources recommended. It still leaked. So I cut the connection again and used the next recommended method, a non-hardening thread sealer. It still leaked. The next time I used thread sealer and tightened the fittings more. When I pressurized the system Wednesday, it still leaked. The filters I installed in our current house have never had a leak. I have concluded that the problem is not me or the way I make the connection, it’s the filter housings themselves. So the next step is to replace the filter housings with a different manufacturer.
On top of that, there are now three leaks in the rest of the water supply lines. The plumber is supposed to work on those on Thursday. The filter connections are going to have to wait. I may simply remove the filter housings and tell the inspector that the branch to the filters is for future use.
Prioritizing has become an important issue for me. There is a lot of work to be done, by me and by contractors. The work that can delay house completion is the work that has to be done first. Other work that can be done later, has to be done later, even if it is necessary work. This is basically critical path analysis. In the case of home construction, some things can proceed in parallel, but a lot has to be done serially; that is, one thing must be done before the next can be done. Identifying those tasks is the important thing right now.
Leah looks at the current state of the house in dismay; there is so much to be done, and she doesn’t see how it’s all going to get done in time. I am aware of all that needs to be done, but I look only at what needs to be done right now. She worries, but I think. If I allowed myself to think about everything that needs to be done, I would probably be paralyzed.
As it is, virtually every waking moment that I’m not doing something else, I am thinking about what needs to be done right now and how I’m going to do it. I go over every step in my head, picturing what I’m going to do. If I did this for a living, I would already know each step and how to do it, so I wouldn’t obsess over it, but this is only the second time I have built a house, so it’s not routine for me.
Right now, the critical path leads to drywall, because so many things depend on having drywall up. Everything I do now is something that has to be done before drywall can be installed. I started out thinking that was just installing insulation, but, of course, that was far too simple. Here’s what had to be done prior to drywall, or at least what I can think of now:
- Put reinforcing blocks behind the shower and tub surrounds to prevent flexing of the fiberglass material.
- Install wood in the walls around the toilets so that grab bars can be mounted.
- Install hurricane ties on the rafters, ceiling joists and wall top plates.
- Seal all the holes drilled in the top and bottom wall plates by the electrician and plumber to keep unconditioned air from leaking in.
- Install vent channels against the roof to let fresh air come in through the soffit vents and not get blocked by insulation.
- Install insulation dams at each rafter vent and where the part of the attic over the house meets the front porch and the garage so that the blown-in insulation isn’t blown out into areas that don’t need insulation.
- Install a blower in the attic to blow hot air from the wood-burning stove in the living room to our bedroom.
- Frame an opening in the hall ceiling to mount the whole-house fan.
- Frame an access opening in the garage ceiling.
- Insulate the walls.
- Cut and fit rounded supports for drywall around the arches over the front windows.
Some of this has been done. Here’s the blower mounted in the attic. The heating and air conditioning contractor is going to install the ductwork, but I’m not sure when.
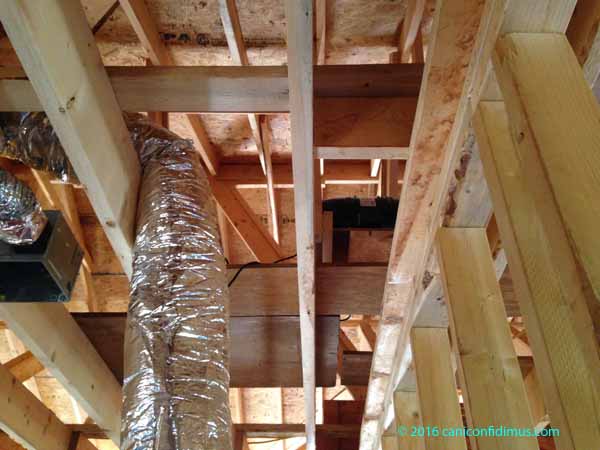
The blower is the black object you can just see to the right of the center of the image. It’s resting on a platform suspended from rafters. The shiny tube hanging down in the picture is for the bathroom exhaust vent.
When I was building the blower support shelf in the attic, I saw this little bird.
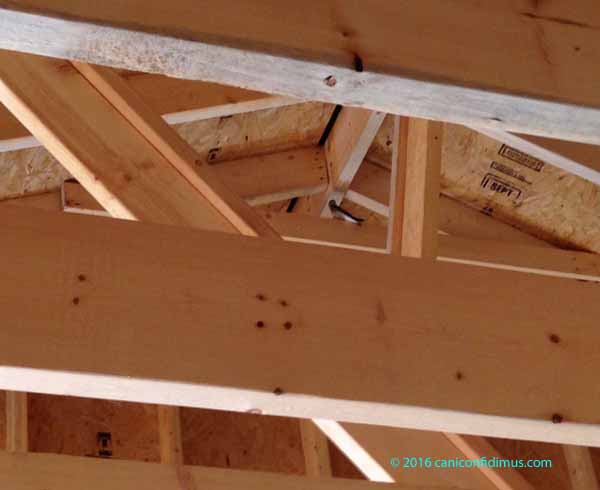
He (or she)is perched just below the ridge beam. It was dark with some white on its breast. Someone more familiar with birds may be able to identify this one. If I had to make a guess, I would say it was a swift. It flitted around, chirping every so often. It went back and forth in the attic over the house, occasionally darting into the attic over the garage. Its behavior reminded me of the hummingbirds that trap themselves in our garage. Later, however, I saw either this bird or one just like it flying towards an open window from the outside. It swerved away when it saw me. I have noticed bird droppings in the house. I’m sure it’s great shelter and it provides lots of potential nesting sites, but, of course, I can’t allow that. Once the drywall is up, there won’t be any access to the attic.
I have put the blocking in the walls to mount grab bars in the bathrooms, and the reinforcing blocks around the tub and shower. I mentioned that earlier. I have sealed almost all the holes in the top and bottom wall plates, but still need to catch a few more. I put in the roof vent channels a couple of weeks ago (injuring my shoulder in the process). I put in some of the insulation dams, but still need to do it between the garage and the rest of the house. And I finished framing for the whole-house fan.
I have been working on insulation for some time now, but on Wednesday I decided to start on the rafter ties. I managed to get about 75 percent of the house done Wednesday, but there is still more to do in the garage than I’ve already done in the house.
This picture shows several of the critical path tasks.
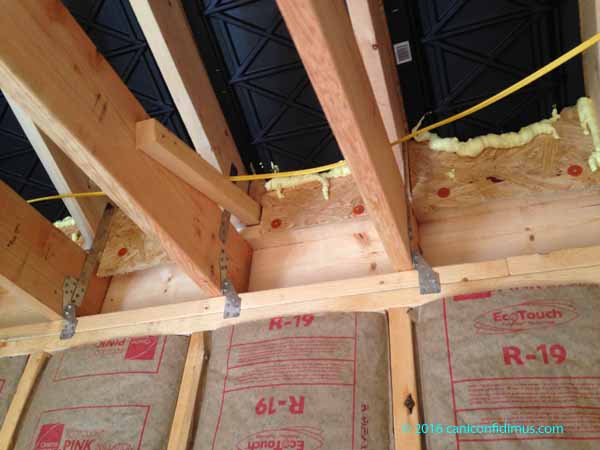
These stud bays have fiberglass insulation bats installed. You can see the black vent channels against the roof, and the insulation dams beneath them (they’re attached with nails that have a red plastic collar). I used expanding foam to seal around the dams. You can also see the rafter ties. In this case, I couldn’t get metal brackets that would normally connect the rafters with the top plate (the horizontal boards that rest on top of the wall studs) because the rafters are too far above the top plate. I ended up using rafter ties to connect the top plate with the ceiling joists, and then flat plates to connect the joists to the rafters.
Hurricane ties are intended to help prevent the roof from blowing off the house in a severe storm. Around here we don’t get the kind of wind that does that very often like they do in coastal areas that are subject to hurricanes, so they aren’t required. But I think they’re a good idea, just in case.
I expect to finish the rafter ties on Thursday. I hope to finish the insulation by the end of the weekend, but that may be optimistic. I’ve already done the easy part. That was putting whole bats into stud bays that are the nominal 16 inches on-center and eight feet high. Now I have to cut and fit a different-sized piece in every other bay, and there are a lot of those.
Also, because of the way the house was framed, there are some wall cavities that I can’t reach to insulate. These isolated cavities are located where interior walls meet exterior walls. I have had to cut out pieces of a stud, stuff in insulation, and then screw another stud to the pieces. There are six of these isolated cavities. I have done three of them. I can do two more, but the remaining cavity is blocked by too much framing. There is a gap that I can see through, so I am going to just spray as much insulating foam as I can into that cavity.
I’m afraid those rounded drywall supports over the arched windows on the front of the house are going to be a problem, but sufficient unto the day is the evil thereof.
The plan now is for the drywall hanger to meet me at the house on Saturday. He can work up his estimate then and tell me when he can start. I hope it’s soon, but that depends not only on his schedule, but mine as well. In another in my long series of laughably optimistic estimates, I had been kind of planning to get the next building inspection by the end of this week. That is obviously not going to happen. But I can’t start drywall until I pass that inspection.